【お困りごと解決コラム01】パーツフィーダーにおけるチョコ停対策の秘訣は、導入後ではなく導入前にあり!
「どうしたらチョコ停が解消するの?」「どんな時にチョコ停は起こるの?」などなど、
みなさんそれぞれのお悩みがあると思います。
そもそも、
・「チョコ停ってなに?」
・「チョコ停ってどんな状況?」
・「チョコ停による影響は?」
というように
「どのような意味なのか」「なにがいけないのか」
がわからないという方もいるかもしれません。
今回の記事では、そんなチョコ停の意味やパーツフィーダーでの
チョコ停対策について解説していきます。
1.チョコ停とは?
「チョコ停」とは、JIS(日本産業規格)にも記載されている一般的な表現です。
生産管理用語であり、「小故障」の通称として紹介されています。
システム全体を停止に至らしめるような重大又は決定的な
故障を大故障(通称としてドカ停),逆に設備の部分的な停止
又は設備の作用対象の不具合による停止で,短時間に回復できる故障を
小故障(通称としてチョコ停)という。
出典:日本工業規格 JIS│Z 8141 : 2001│生産管理用語 f)設備管理 1)設備管理 6108 故障
まずは、「チョコ停」とはどのような状況を指す用語なのかを把握する必要があります。
現場で使われている「ドカ停」の用語の意味もあわせて確認していきましょう。
A. チョコ停
設備の部分的な停止のことで、部品を交換したりせず、調整することで復旧できる故障です。
短時間で回復できることも特徴ですが、同じ原因での停止が何度も発生してしまう場合もあります。
チョコ停は、1回あたりの復旧までの時間は短時間ですが、何度も発生してしまうと、
運転効率に影響を及ぼす可能性は大いに考えられます。
B. ドカ停
生産ラインなどの大規模なシステムの一部としての設備の故障で、
システム全体を停止させてしまうような重大な故障です。
ドカ停は、部品破損や調整では解決できない故障となる為、
長時間(数時間~数日)運転が停止してしまうと考えられます。
2.チョコ停とパーツフィーダー
パーツフィーダーとは、大量の「ワーク」をピックアップしやすい姿勢に整列させる装置です。
装置単体での運転時はもちろん、次工程との関係で「チョコ停」が発生する場合があります。
「ワーク」を供給する設備で発生する「チョコ停」は、
・「どんな原因で発生するのか?」
・「どんな解決方法があるのか?」
新しい設備を検討する際に必ず課題となる内容だと思います。
そんな永遠の課題、パーツフィーダーでのチョコ停について解説していきます。
A. 従来のパーツフィーダー(振動フィーダー)について
ワークを入れたボウル等に振動を加えることでワークを整列・搬送させる装置です。
様々な形状、素材のワークの整列が可能で、パーツフィーダーの大部分を占めています。
ゴム素材、特にOリングのような柔らかく形状が不安定な物(線径が細く、外径が大きい)
に関しては、整列・搬送が難しく、「チョコ停」が発生し易いという課題もあります。
汎用性が高いので、機器選定の際には、得意な「形状」「素材」のワークを見極める必要があります。
B. 従来のパーツフィーダー(振動フィーダー)での「チョコ停」の原因と解決方法
従来のパーツフィーダーでの「チョコ停」の原因はなにがあるのでしょうか?
解決方法とあわせて解説していきます。
①静電気
パーツフィーダーは、振動でワークを整列させるため、摩擦と剥離を繰り返しながら
各工程を流れ、静電気を蓄積しやすくなっています。
ワーク同士で擦れ合い、摩擦帯電が発生するので、各工程で除電できるように
イオナイザー(静電気除去器・除電器)を設置する対策が有効です。
②ボウルの汚れ
ボウルの表面が汚れている場合、スムーズな部品供給が行われず、
チョコ停が発生する場合があります。
チョコ停を起こさないよう、ボウル内を定期的に清掃する必要があります。
③装置自体の不具合
「経年劣化で振動が弱くなっていてワークがうまく進まない」
「長期間運転でボール内のコーティングが剥離しワークがうまく進まない」
など、装置自体にチョコ停の原因がある場合もあります。
この場合は、装置自体の改善を検討する必要があります。
C. 「サイダ・UMS製 Oリング整列供給ユニット」について
振動ではなくエアーの力によりワークを整列・搬送させる装置です。
振動ではなくエアーの力によりワークを搬送するため、ゴム素材の影響を受けにくく、
Oリングのような柔らかく形状が不安定な物(線径が細く、外径が大きい)の搬送に適しています。
Oリング整列供給ユニットも従来のパーツフィーダー(振動フィーダー)と同様の課題により
「チョコ停」の発生リスクはありますが、発注前の「事前テスト」にて排出可否を
『事前に検証』するため、実際に納品する装置では「チョコ停」のリスクが低くなっています。
例えば、簡易的な設定ではチョコ停が「3900個中 1個」発生したワークも、
事前テストにて仕様を細かく設定することによって「10000個中 1個未満」にしています。
事前テスト調整にてあらかじめチョコ停率の低い設定を選定し、
製品版への設計に反映させることが可能です。
D. 「サイダ・UMS製 Oリング整列供給ユニット」での「チョコ停」の対策
Oリング整列供給ユニットでの「チョコ停」対策はどんな内容なのかを解説します。
①供給可否テスト
サイダ・UMSでは無料の供給可否テストを事前に行うことによって、
ワーク毎に最適な仕様を検討し、ワーク専用の部品を 設計・製作 しています。
発注前に最適な条件を検証することによって、「チョコ停」のリスクを回避することができます。
供給可否テストにて供給可能と判断された場合は
・弊社規格に基づく各時間当たりの排出個数
・設定空気圧等
・テスト時の動画
をレポートにまとめ、提出させていただきます。
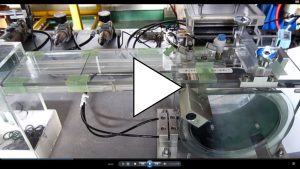
1.全体俯瞰動画
2.整列イメージ動画
3.テスト結果レポート
事前に仕様をしっかり決めている為、「リピート品として全く同じ装置が欲しい!」
となった場合でも問題なく対応可能です。
②出荷テスト
出荷テストでは発注前の供給可否テストと同様に、最適な条件を検証・設定することによって、
「チョコ停」のリスクを回避することができます。
出荷検査時の「各時間当たりの排出個数」「空気圧」「スピードコントローラーの設定」
の推奨値も、納品時に一緒に提出しています。
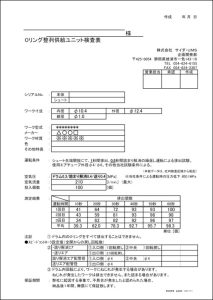
テスト結果レポート
3.「Oリング整列供給ユニット」導入に関するご相談について
弊社では実際にご検討中のサンプルワークにて「供給可否テスト」を実施させていただきます。
ご検討中のワークサイズをご提示いただければ、「供給可否テスト」のご案内をさせていただきます。
Oリング供給でお困りの方はもちろん、Oリング以外でお困りの方も、まずは一度ご相談ください!
————————————————
<平野 遼香>
Oリング整列供給ユニット 営業窓口担当。パーツフィーダーについて日々勉強中。ユーザーのみなさんが“知りたいこと”をお伝えできるよう、学んだ内容を情報発信していきます!最近の趣味は、パン作り。
ダウンロード
ご希望の方は下記のフォームよりダウンロードをお願いいたします。
☑Oリング整列供給ユニットの導入事例
☑ワークの供給実績
☑シュート部(ストレート部)の段取替え
資料一覧
・カタログ
・(導入事例01)車載カメラ用レンズの組込みユニット
~導入後の成果(サイクルタイム等)掲載中~
・Oリング整列供給ユニット 供給実績一覧表
(内径、線径(厚さ)、外径、材質)
・(動画)段取り替え手順(シュート部取り換え手順)